Peak Downs Mine Coal Thickener Bridge Replacement
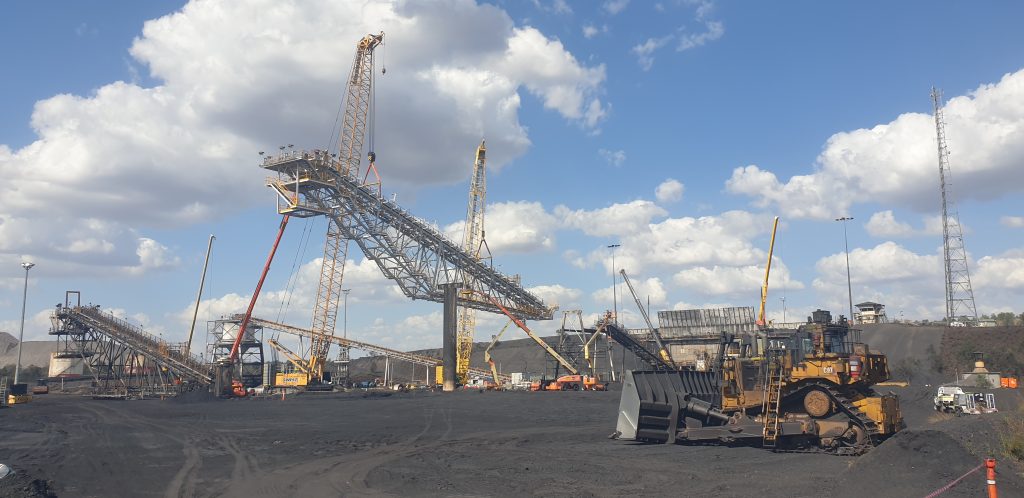
Peak Downs Mine (PDM), operated by BHP Mitsubishi Alliance (BMA), is a coal mine located in Central Queensland, approximately 40 kilometers southeast of Moranbah, or about a 35-minute drive. The project site is situated within the operational Coal Handling and Preparation Plant (CHPP), specifically on the western side of the CHPP, above the Coal (Froth) Thickener. Due to the extensive wear on the existing Coal Thickener Bridge, which has reached the end of its operational life, replacement is now necessary. This critical structure supports a wide range of essential services, including mechanical drives, hydraulic systems, electrical and control systems, the flocculant dosing system, coal slurry and water pipelines, and compressed air infrastructure.
Additionally, the existing bridge provides suspension for the feedwell and thickener raking system, making it an integral part of the CHPP’s overall functionality. As part of this project, the goal is to replace the Coal Thickener Bridge structure and associated infrastructure. To achieve this, all existing equipment will be reinstalled, and any necessary new piping, valves, supports, and cabling will be included as part of the upgrade. In order to minimise downtime, this critical work will be scheduled during the planned FY24 shutdown to ensure the Coal Thickener is restored to full operational status.
This project is crucial for maintaining the reliability and efficiency of the CHPP at Peak Downs Mine, supporting its continuous production. CE Group, as an experienced electrical mining contractor, has been engaged to carry out the electrical and instrumentation (E&I) scope of work. Throughout the project, CE Group will ensure that all electrical systems are replaced, tested, and commissioned in line with industry standards and safety regulations. Moreover, their involvement will support the seamless integration of the newly installed infrastructure, ensuring minimal disruption to the CHPP’s operations.
In addition, CE Group will provide ongoing support during the commissioning phase to guarantee that all systems are functioning optimally. Ultimately, the successful replacement of the Coal Thickener Bridge will enhance the operational efficiency of Peak Downs Mine, ensuring that the CHPP continues to meet production targets while maintaining high standards of safety and performance.
Carmichael Mine E&I Belt Filters
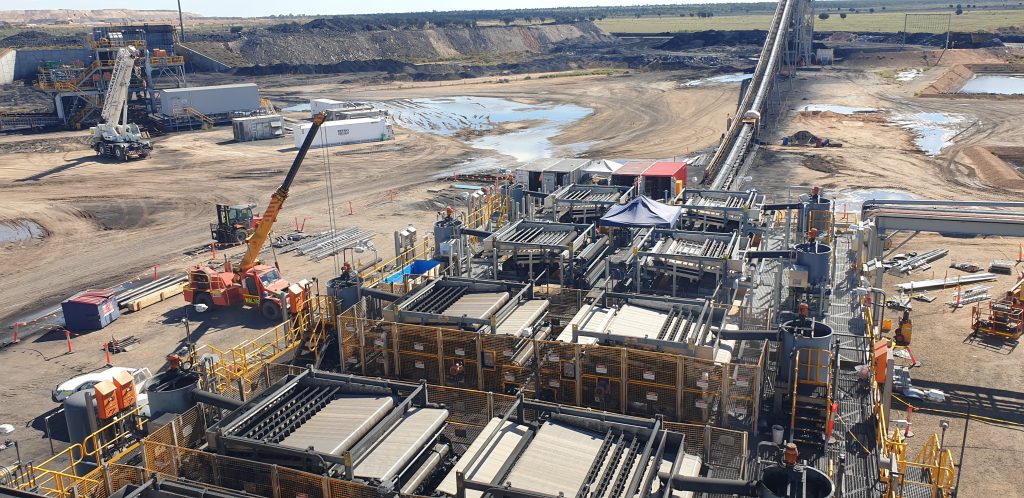
This project involved the installation of four belt filter presses to complement the existing four presses currently operating within the Coal Preparation Plant (CPP) at the Adani Mine.
BMA Goonyella Riverside Mine Switchboard Install Phase 2
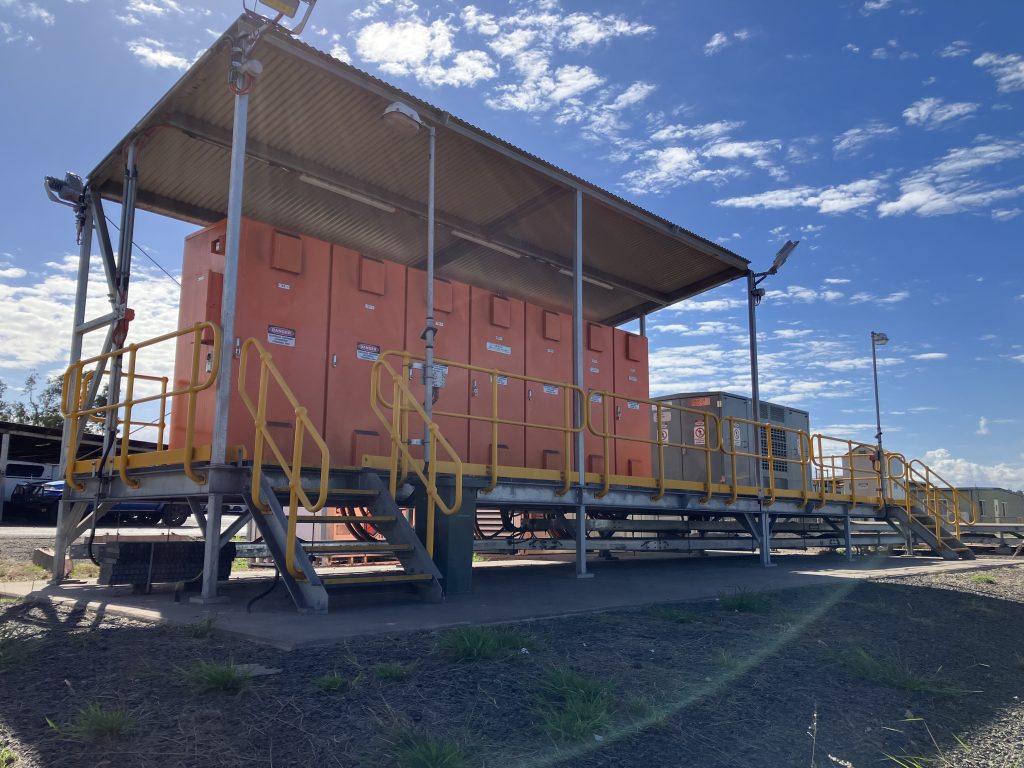
Goonyella Riverside Mine (GRM), a key coal mining operation in the Bowen Basin, is located about 30km north of Moranbah and 190km southwest of Mackay. As a leading electrical mining contractor, CE Group was engaged to upgrade the mine’s Coal Preparation Plant 1 (CPP1) Fine Rejects Dewatering system. This project aimed to rectify a plant bottleneck, increasing production rates and improving system reliability.
The upgrade involved replacing the existing dewatering screen with larger dual screens. This enhancement was critical to addressing a single point of failure (SPF) within the system, which previously halted production when unavailable. By upgrading the system, the mine would not only boost productivity but also ensure redundancy, a key requirement for uninterrupted operations.
As part of this major SMP (Structural, Mechanical, and Piping) and Electrical & Instrumentation (E&I) overhaul, CE Group undertook a wide range of services. These included the supply and installation of new Motor Control Center (MCC) cells, crucial for ensuring the safe and efficient operation of various electrical systems. Additionally, CE Group handled the supply and installation of all pneumatic equipment, power and control cabling, and instrumentation across the site.
The project also required the installation of remote I/O panels and remote local control stations, enhancing the mine’s operational efficiency. These installations allowed for better control and monitoring of key systems, ensuring that production could continue smoothly without unnecessary interruptions.
Throughout the project, CE Group’s extensive expertise as an electrical mining contractor played a vital role in delivering high-quality results. The team worked closely with key stakeholders to ensure the project was completed on time and within budget, all while maintaining strict safety standards.
This successful collaboration at Goonyella Riverside Mine further solidifies CE Group’s reputation as a trusted electrical mining contractor. Their ability to manage complex electrical and instrumentation projects in challenging mining environments ensures that clients can achieve improved operational outcomes while maintaining safety and efficiency.
As a leading electrical mining contractor, CE Group was engaged to upgrade the mine’s Coal Preparation Plant 1 (CPP1) Fine Rejects Dewatering system.
BMA Goonyella Riverside Mine Fire & High Pressure Water Upgrade
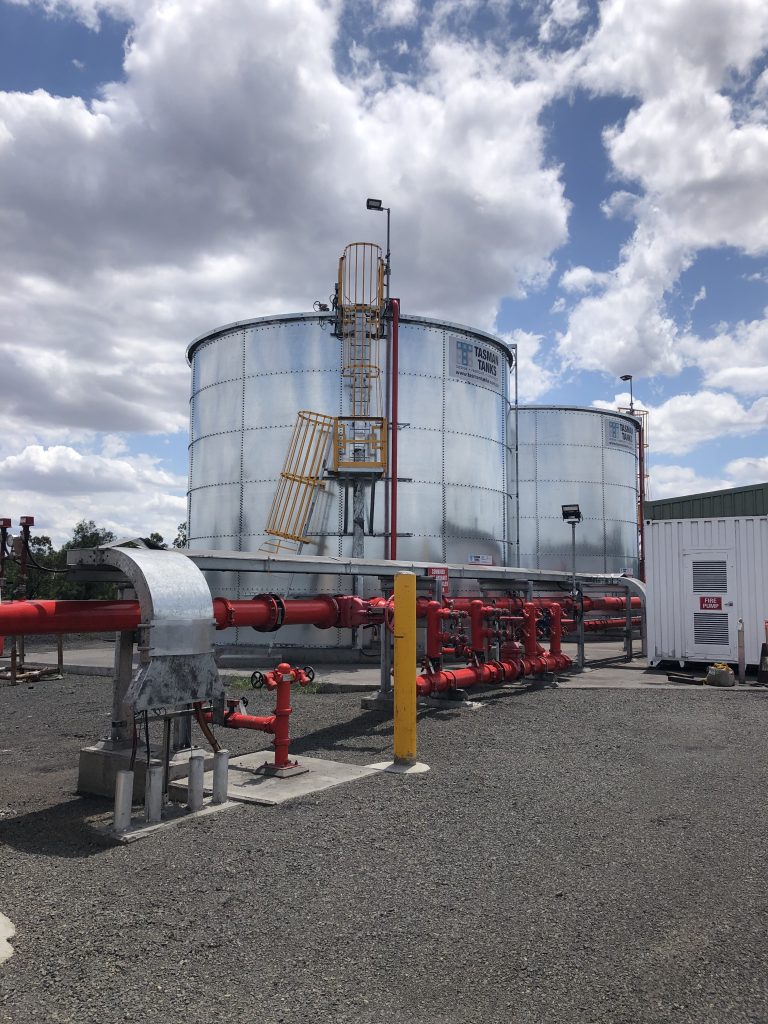
BHP Mitsubishi Alliance (BMA) operates the Goonyella Riverside Mine (GRM), located approximately 35 kilometres north of Moranbah in Queensland. This mine produces around 7.5 million tonnes per annum (Mtpa) of high-quality metallurgical coking coal, which is sold both domestically and exported through Mackay. As a critical supplier of this valuable resource, ensuring the mine’s operational efficiency is paramount.
Tallawarra B Power Station
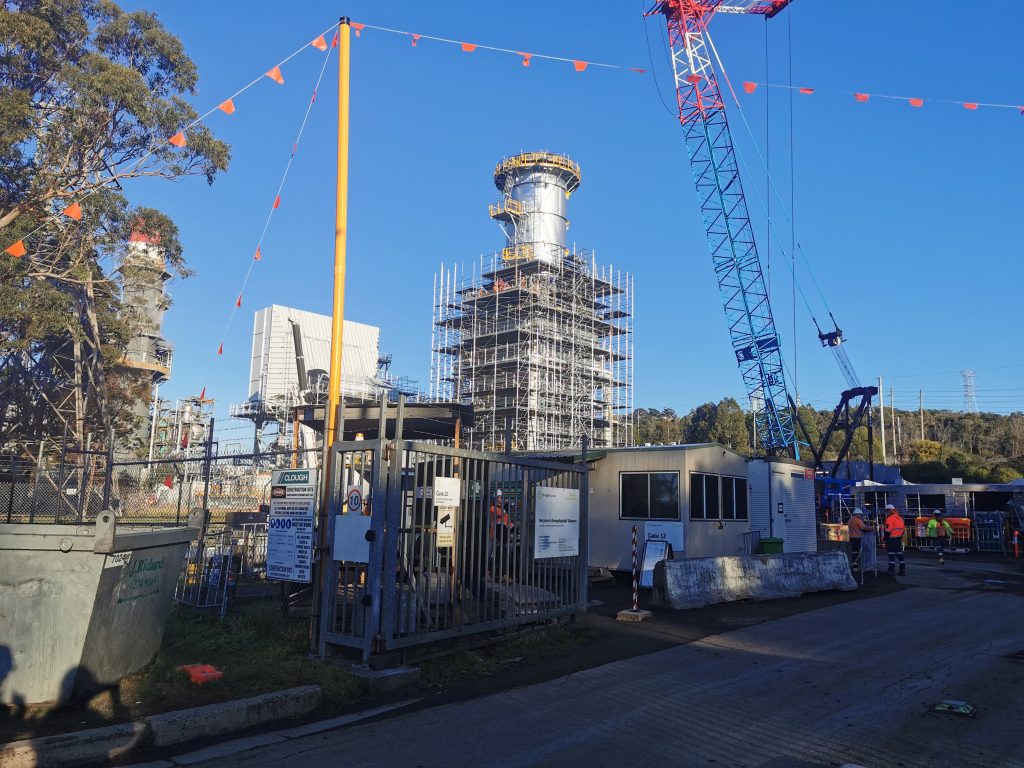
Tallawarra Stage B is a 300+ MW expansion of the existing Tallawarra A power station, involving the construction of a 420MW Open Cycle Gas Turbine Power Plant.
Saraji Mine Workshop Extension
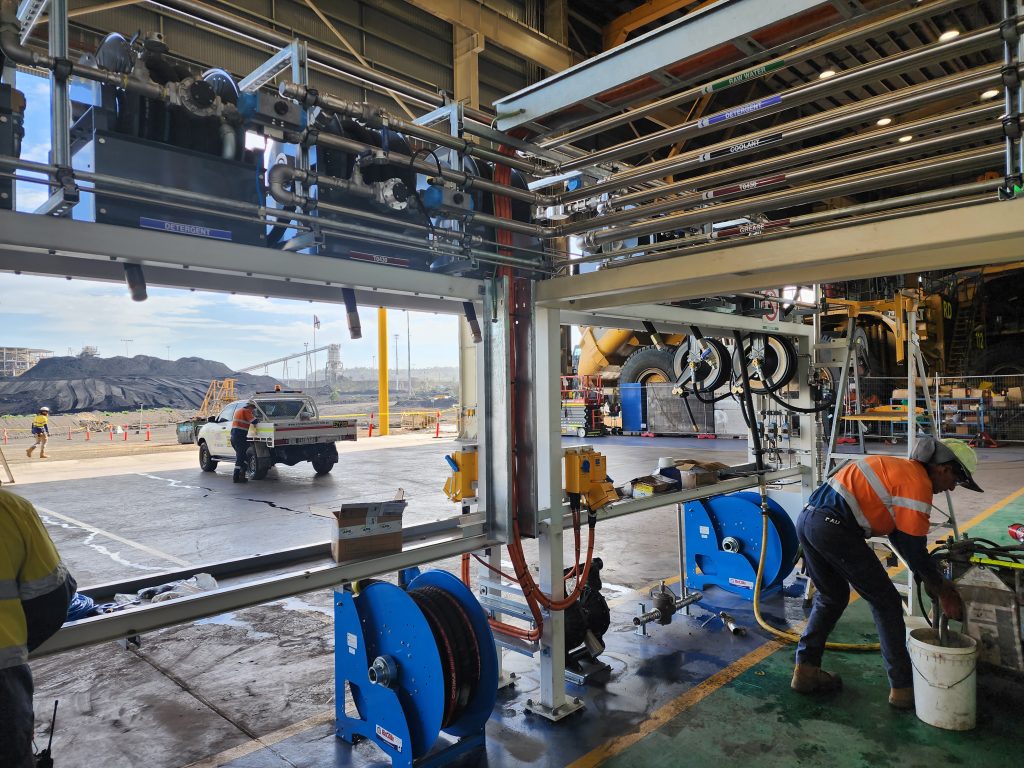
CE Group, a leading electrical mining contractor, was engaged by Walz Group to carry out significant electrical works at Saraji Mine.
GRM Riverside Rejects System Refurbishment and Remediation

CE Group were engaged to undertake the rewiring and replacement electrical equipment, cabling and devices on the R1 conveyor, 300T Rejects Bin/Belt Feeder and R2 Conveyor. Electrical connection and assistance for new Radial Stacker, decommission R3 Conveyor and Travelling Rejects Stacker.
Dalrymple Bay Coal Terminal (DBCT) Stacker Project
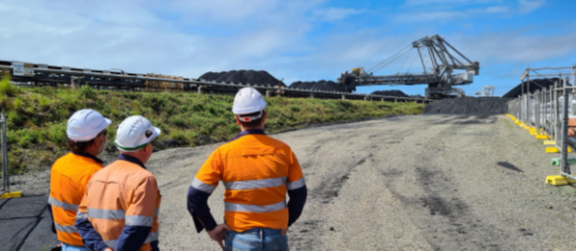
Dalrymple Bay Coal Terminal, a critical part of Queensland’s coal export infrastructure, is undergoing a significant upgrade to sustain its operational efficiency. As part of this effort, the terminal is replacing its existing rail-mounted stacker machine (ST1) with a newly designed Stacker (ST1A). This upgrade is essential to improve the terminal’s capacity and enhance its long-term reliability.
BMA Goonyella Riverside Mine Dewatering Screens Upgrade
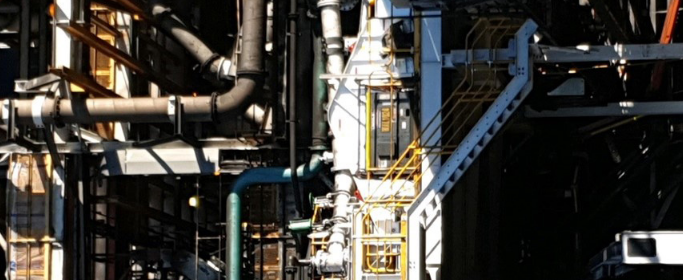
Goonyella Riverside Mine (GRM), a key coal mining operation in the Bowen Basin, is located about 30km north of Moranbah and 190km southwest of Mackay. As a leading electrical mining contractor, CE Group was engaged to upgrade the mine’s Coal Preparation Plant 1 (CPP1) Fine Rejects Dewatering system. This project aimed to rectify a plant bottleneck, increasing production rates and improving system reliability.
The upgrade involved replacing the existing dewatering screen with larger dual screens. This enhancement was critical to addressing a single point of failure (SPF) within the system, which previously halted production when unavailable. By upgrading the system, the mine would not only boost productivity but also ensure redundancy, a key requirement for uninterrupted operations.
As part of this major SMP (Structural, Mechanical, and Piping) and Electrical & Instrumentation (E&I) overhaul, CE Group undertook a wide range of services. These included the supply and installation of new Motor Control Center (MCC) cells, crucial for ensuring the safe and efficient operation of various electrical systems. Additionally, CE Group handled the supply and installation of all pneumatic equipment, power and control cabling, and instrumentation across the site.
The project also required the installation of remote I/O panels and remote local control stations, enhancing the mine’s operational efficiency. These installations allowed for better control and monitoring of key systems, ensuring that production could continue smoothly without unnecessary interruptions.
Throughout the project, CE Group’s extensive expertise as an electrical mining contractor played a vital role in delivering high-quality results. The team worked closely with key stakeholders to ensure the project was completed on time and within budget, all while maintaining strict safety standards.
This successful collaboration at Goonyella Riverside Mine further solidifies CE Group’s reputation as a trusted electrical mining contractor. Their ability to manage complex electrical and instrumentation projects in challenging mining environments ensures that clients can achieve improved operational outcomes while maintaining safety and efficiency.
As a leading electrical mining contractor, CE Group was engaged to upgrade the mine’s Coal Preparation Plant 1 (CPP1) Fine Rejects Dewatering system.
Hail Creek Industrial Area Upgrade – Warehouse
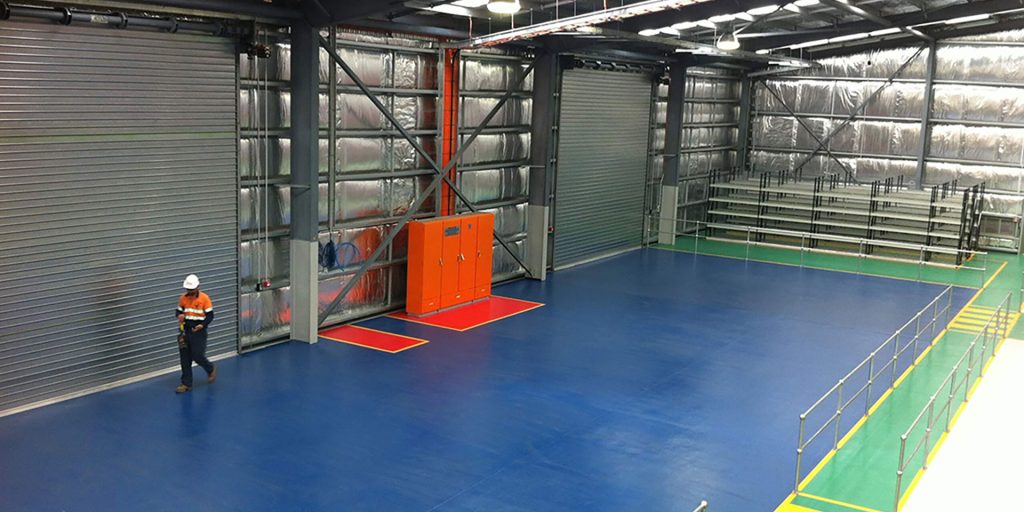
The Hail Creek IAU – Warehouse project saw CE Group continue its support of the Mining Industry. The project involved the supply, installation, testing and commissioning of electrical works for the 2.750m2 warehouse at Hail Creek Mine .